DCS vs. PLC: Compreendendo as diferenças e aplicações
Introdução
No domínio da automação industrial, duas tecnologias-chave se destacam por seu papel fundamental no controle e monitoramento de processos: Sistemas de Controle Distribuído (DCS) e controladores lógicos programáveis (CLP). Ambos servem a propósitos distintos e encontram aplicações em vários setores, tornando crucial compreender suas diferenças, pontos fortes e casos de uso ideais. Este artigo investiga as especificidades de cada tecnologia, comparando suas aplicações, arquiteturas, capacidades de controle e escalabilidade, e destacando suas respectivas vantagens e desvantagens.
O que é DCS?
Um sistema de controle distribuído (DCS) é um sistema de controle especializado usado predominantemente em indústrias de processo, como petróleo e gás, processamento químico e geração de energia. Ele foi projetado para gerenciar processos complexos que envolvem múltiplas malhas de controle e sinais analógicos.DCSa arquitetura normalmente consiste em vários controladores autônomos distribuídos por uma instalação ou planta. Esses controladores se comunicam entre si e com um sistema de supervisão central por meio de uma rede de alta velocidade.
Principais recursos deDCS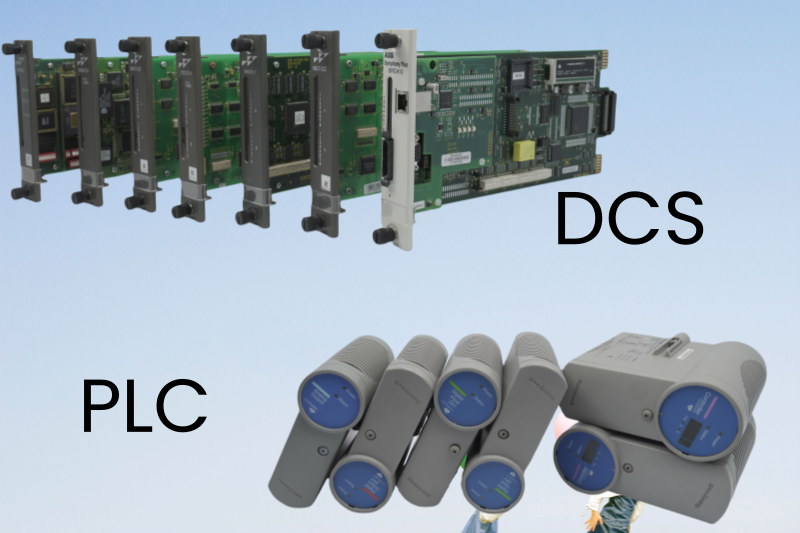
Monitoramento Centralizado:DCSOs sistemas fornecem uma plataforma centralizada para monitorar e controlar todos os processos dentro de uma planta. Essa centralização garante um gerenciamento coeso e operações simplificadas.
Rede de alta velocidade: Comunicação emDCSsistemas ocorre em uma rede de alta velocidade, permitindo aquisição e controle de dados em tempo real. Isso é crucial para manter a integridade do processo e a eficiência operacional.
Capacidades de controle avançadas:DCSos sistemas são projetados para lidar com algoritmos de controle complexos e técnicas avançadas de controle de processo, que são essenciais para otimizar o desempenho do processo e alcançar alta precisão.
Redundância e Confiabilidade:DCSos sistemas geralmente incluem controladores e caminhos de comunicação redundantes para garantir alta confiabilidade e minimizar o tempo de inatividade em ambientes industriais críticos.
O que é CLP?
Um controlador lógico programável (CLP) é um computador digital robusto projetado para automatizar processos eletromecânicos em indústrias de manufatura discreta.CLPsdestacam-se em aplicações onde as tarefas são repetitivas e exigem controle preciso sobre máquinas e processos. Eles são amplamente implantados em setores como fabricação automotiva, embalagens e linhas de montagem, onde a confiabilidade e o desempenho em tempo real são essenciais.
Principais recursos do PLC
Design modular:CLPspossuem design modular, permitindo fácil customização e expansão. Esta flexibilidade é particularmente benéfica para projetos de automação de pequeno e médio porte.
Controle em tempo real:CLPssão capazes de fornecer controle em tempo real e tempos de resposta rápidos, essenciais para processos de fabricação discretos que envolvem operações rápidas e sequenciais.
Facilidade de programação:CLPs são conhecidos por suas interfaces de programação fáceis de usar, que facilitam o desenvolvimento e a modificação de programas de controle por técnicos e engenheiros.
Durabilidade: Projetados para resistir a ambientes industriais adversos, os CLPs são robustos e confiáveis, garantindo desempenho consistente mesmo sob condições adversas.
Principais diferenças
Formulários:
DCS: Usado principalmente em indústrias onde o controle e o monitoramento contínuos de operações em grande escala são essenciais. Os exemplos incluem fábricas de produtos químicos, refinarias e usinas de energia.DCSOs sistemas são ideais para processos que exigem controle meticuloso de inúmeras variáveis e onde o custo do tempo de inatividade é alto.
CLP: Ideal para indústrias de manufatura discreta onde as tarefas são discretas e envolvem controle sequencial. As aplicações comuns incluem sistemas de transporte, linhas de montagem robóticas e manuseio de materiais.CLPs são adequados para aplicações que exigem operações de alta velocidade e mudanças frequentes na lógica de controle.
Arquitetura do sistema:
DCS: Arquitetura centralizada com múltiplos controladores distribuídos pela planta. Cada controlador gerencia seções específicas do processo e se comunica através de um sistema central de supervisão. Esta natureza distribuída permite o manejo eficiente de processos complexos e alta integração de diversas funções de controle.
CLP: normalmente opera como uma unidade autônoma ou como uma pequena rede de controladores. Os CLPs estão diretamente conectados a sensores, atuadores e outros dispositivos de controle, muitas vezes organizados de forma modular. Essa modularidade proporciona flexibilidade no projeto do sistema e facilita a expansão ou reconfiguração do sistema conforme necessário.
Capacidade de controle:
DCS: Otimizado para lidar com processos complexos envolvendo sinais analógicos e malhas de controle contínuas.DCSoferecem recursos robustos para controle preciso, aquisição de dados e integração com estratégias de controle avançadas. Eles estão equipados para gerenciar um grande volume de dados e fornecer controle sofisticado de processos.
CLP: Adequado para tarefas de controle discreto onde operações lógicas, sequenciamento e temporização são essenciais.CLPÉ excelente na execução de operações baseadas em lógica e no gerenciamento de sinais de E/S digital (entrada/saída). Eles são particularmente eficazes em aplicações onde as tarefas de controle são repetitivas e simples.
Escalabilidade:
CCS: Escalável de sistemas pequenos a grandes, capaz de gerenciar extensas redes de controladores e dispositivos em uma ampla área.DCSas arquiteturas são projetadas para acomodar processos industriais complexos com alta confiabilidade e redundância. Eles podem integrar perfeitamente pontos de controle adicionais e expandir à medida que o processo cresce.
CLP: Modular e escalável, permitindo fácil expansão ou modificação com base em requisitos específicos da aplicação.CLPos sistemas são adaptáveis a vários ambientes industriais e podem ser integrados em ambientes de automação existentes. Essa escalabilidade os torna adequados para uma ampla gama de aplicações, desde pequenos sistemas autônomos até instalações complexas em rede.
Aplicativos e casos de uso
DCS Formulários:
Indústrias de Processo Contínuo: DCSé amplamente utilizado em indústrias como refino, petroquímica e geração de energia, onde o controle e o monitoramento contínuos são cruciais.
Sistemas de controle de alta integridade: Aplicações que exigem sistemas de controle de alta integridade com redundância integrada para maior confiabilidade se beneficiam significativamenteDCS. Isto inclui infraestruturas críticas onde a falha do sistema pode ter consequências graves.
Estratégias de Controle Avançadas: A integração com estratégias de controle avançadas, como algoritmos de otimização, manutenção preditiva e monitoramento de processos em tempo real, é um ponto forte doDCSsistemas.
CLP Formulários:
Operações de Fabricação Discreta:CLPs são amplamente utilizados em linhas de montagem automotiva, embalagens e operações de manuseio de materiais, onde as tarefas são discretas e envolvem controle preciso.
Controle de Máquinas: O controle de máquinas e equipamentos que exigem tempo preciso, sequenciamento e operações baseadas em lógica é uma aplicação primária deCLPS.
Programação Flexível: CLPs oferecem recursos de programação flexíveis adequados para uma ampla gama de tarefas de automação industrial, tornando-os ferramentas versáteis em vários ambientes de fabricação.
Vantagens e desvantagens
DCS Vantagens:
Superior para gerenciar processos de grande escala:DCSos sistemas se destacam no gerenciamento de processos contínuos e de grande escala com requisitos de controle complexos.
Alta confiabilidade e tolerância a falhas: A arquitetura tolerante a falhas com controladores e vias de comunicação redundantes garante alta confiabilidade.
Otimização integrada e aquisição de dados:DCSos sistemas vêm com recursos integrados para otimização de processos, aquisição de dados e integração perfeita com sistemas de nível empresarial.
DCS Desvantagens:
Maior investimento inicial: A complexidade da arquitetura e a natureza especializada das aplicações resultam num investimento inicial mais elevado.
Requer engenheiros qualificados: Projetando, programando e mantendoDCSsistemas exigem engenheiros qualificados com conhecimento especializado.
CLP Vantagens:
Econômico para projetos de pequeno e médio porte:CLPs oferecem uma solução econômica para projetos de automação de pequeno e médio porte.
Design modular para fácil personalização: O design modular facilita a personalização, expansão e integração em sistemas de controle existentes.
Interface de programação acessível: A interface de programação simples é acessível a técnicos e engenheiros com formação básica.
CLP Desvantagens:
Escalabilidade limitada para grandes sistemas:CLPos sistemas podem enfrentar limitações ao serem ampliados para sistemas muito grandes com extensos requisitos de E/S.
Menos eficiente com controle analógico complexo: Gerenciar controles analógicos complexos é menos eficiente comCLPé comparado aDCSsistemas.
Conclusão
Em resumo, escolher entreDCSeCLPdepende dos requisitos operacionais específicos e das características do processo industrial.DCSé ideal para indústrias que exigem alta confiabilidade, operação contínua e estratégias de controle complexas.CLPs, por outro lado, se destacam em ambientes de fabricação discretos onde flexibilidade, escalabilidade e sequenciamento preciso são fundamentais.
A compreensão dessas diferenças permite que operadores industriais, engenheiros e tomadores de decisão façam escolhas informadas ao implementar soluções de automação. Ao aproveitar os pontos fortes deDCSeCLPtecnologias, as indústrias podem otimizar a eficiência, aumentar a produtividade e manter a competitividade no cenário de mercado dinâmico atual.